A社の活動紹介 <TPM優秀賞 カテゴリーA受賞>
A社の事例では、8本柱のうちもっとも基礎となる個別改善と自主保全の柱の活動を紹介する
従業員数は約300名
主な事業 自動車電装品用アルミダイカスト部品、ダイカスト用金型、アルミ合金鋳物
●TPMの取組み背景
受身体質からの脱却を図り、1人ひとりが技術・品質を追求する会社を目ざす
●TPMのねらいと目標
「高品質で安定した生産体制の構築」、「要求に応えられる技術力の向上」をTPMのねらいとし、発生不良 5%未満 、営業利益率 5%以上をTPMの目標とする
●TPM推進組織と運営
会社や部門の方針のもと、柱ごとに専門部会を設置し、各部会で、取組みテーマ、活動内容を定め、課やグループ単位での活動のフォロー、社長診断などを行いながら目標達成を目ざす
個別改善の活動
どのように進めたのか
A社では、活動のねらいを次のように定めた。
① 16大ロスを明確に定義してロス金額を明らかにし、認識を共有する
② ロス金額の多いテーマから改善に取り組む
③ 原理原則に基づいた分析からの改善を定着させる
そして、次のように進めた
(1)16大ロスを明確に定義してロス金額を明らかにし、認識を共有するために、ロス・コストマトリクスを作成した
(2)16大ロスのロス内容を社内で共有し、柱ごとに主に改善するロスを決定
個別改善の専門部会では、16大ロスの内の8つのロス(歩留まりロス、速度低下ロス、エネルギーロス、自動化置換ロス、
編成ロス、段取り調整ロス、管理ロス、動作ロス)を担当し、活動を推進する
(3)改善計画書を作成し、取り上げたテーマの改善目標、方策、スケジュール進捗などをフォロー
<活動事例 :フラックス処理時に発生するメタルロス削減>
材料歩留りロス(アルミ酸化物)を現状34.6Kg/回から33%削減(目標達成)
個別改善の成果
各工場で設備総合効率が向上し、全社ロス排除金額(累計)を積み上げることができた。
・個別改善活動を通じて、経験則にもとづく対策から脱却し、理論に基づいた要因分析により真の原因をつかもうとする意識が芽生えた
・ロスと認識していなかった時間について、16大ロス分析で時間と金額を明確にし、共有認識することでコスト意識が強くなった
自主保全の活動
どのように進めたのか
A社では、「油、水、アルミバリ、ショット材で汚れた設備、周辺環境をクリーンにし、働きやすく改善意欲の高い工場にする」「設備の信頼性を高めて、あらゆるロスを低減・排除する」を目指す姿とし、「人と設備の体質改善」と、「通路砂漠化(飛散ゼロ)」 にねらいを定めて活動を行った。
- 自主保全のステップ展開を活用し、職制によるモデルから始め、課でのモデル展開をした後、全ての設備を対象に活動した
- QC手法による改善事例、ワンポイントレッスンによる教育・活動ミーティングを行い、知識の修得を図った
<各ステップ合格診断までの流れ>
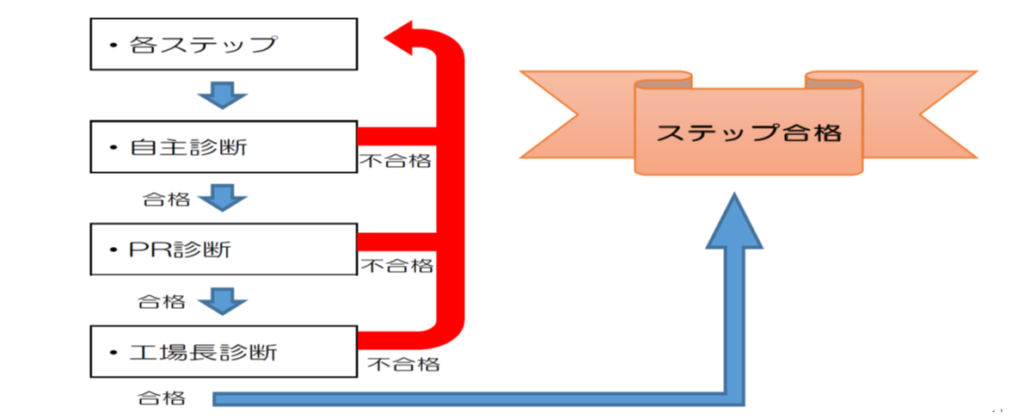
<活動事例<バリ飛散対策(清掃ロス)>
・清掃時間短縮と設備周辺の「砂漠化」(飛散ゼロ)を目標に活動
・飛散箇所の特定を行い、設備周辺のバリ等の飛散面積を調査のうえ、カバー設置を重点に行った。
結果、バリ飛散面積0(目標達成)、清掃時間も、目標にわずか2分未達だが47分にまで短縮
自主保全の成果
(1)設備総合効率は、60%から66%に向上
(2)飛散対策のための辛い姿勢の清掃が減り、楽になる、清掃・型交換時等に作業服の汚れが少なくなり洗濯が楽になる、
といった働く人の困りごとが解決し、働く環境が改善
(3)設備部品のメカニズムの学習を通じ、異常発生時には現象報告だけでなく想定される部位報告まで行えるようになる
など、人材育成の観点でも効果
TPM活動成果(例)
TPM活動の目標としていた、発生不良(不良率)の低減や、営業利益率の向上などの成果を上げた