優秀改善事例全国大会
発表企業のご紹介(2023年度)
本ページでは2023年度優秀改善事例全国大会で発表を予定いただく発表者様の一部をご紹介させていただきます。
発表のポイント、改善に至るまでの苦労や工夫、当日に向けた抱負などをぜひご覧ください!
A-1 トヨタ自動車株式会社 森永 弘志さん
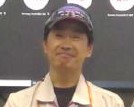
Q1.業務内容と担当業務の経験年数
保全業務・26年
Q2.改善に至るまでの苦労や工夫
改善内容を検証する際に、いかに生産に影響を与えないよう
データを収集するか悩みました。
オフラインで検証する為の治工具・測定機器を製作し検証を重ねた結果、
今回の改善事例に繋げることが出来たと思います。
Q3.大会への意気込み
他企業の皆様に少しでも弊社の改善事例が解りやすく伝わる
様に発表したいと思います。
A-2 ダイキン工業株式会社 小高 範明さん
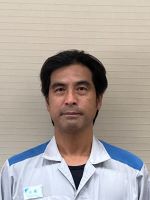
Q1.業務内容と担当業務の経験年数
製造品質支援・20年
Q2.改善に至るまでの苦労や工夫
慢性不良は根深く、内部が確認出来ない事で、アプローチが難しかったが、
定量データを集め手法を活用し、5ゲンに基づき、
ひとつづつ明らかにすることで解決に至ることが出来た。
Q3.大会への意気込み
定量評価からデータの傾向をつかみ、5ゲンに基づき
細やかに分析・解析を行った結果、ゼロ件を達成した事例です。
社内の教育資料にしようと思う内容となっています。ぜひお聞き下さい。
A-3 UBE株式会社 高橋 弘一さん
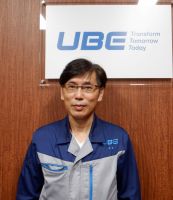
Q1.業務内容と担当業務の経験年数
保全業務・12年
Q2.改善に至るまでの苦労や工夫
設備故障に対して、理論的な探求を通して原因を特定したこと。
理論的な探求とコストを意識した対策の実現を行った。
Q3.大会への意気込み
「故障解析」手法を広くご理解いただくことで、
設備故障の真因をスムーズに特定し対策に結び付けていただければと思う。
A-4 アイシン軽金属株式会社 名村 太一さん
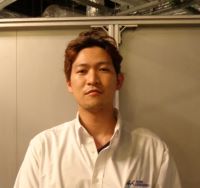
Q1.業務内容と担当業務の経験年数
段取り業務・7年
Q2.改善に至るまでの苦労や工夫
今回の改善事例は職場内での、
やりにくい作業を全員で改善案を出しながら進めてきた事例です。
工夫点は誰でも簡単に調整ができる事です。
Q3.大会への意気込み
今回初めての全国大会ですが、
皆さんに分かって頂ける様にしっかりと自信をもって説明します。
A-5 トヨタ自動車東日本株式会社 今井 嘉祐さん
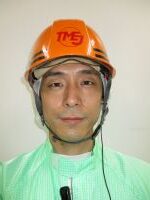
Q1.業務内容と担当業務の経験年数
保全業務・16年
Q2.改善に至るまでの苦労や工夫
当たり前の改善が通用しない現実に対し、
どうしたら出来るかを皆で悩み抜き、具現化する事が難しかった。
Q3.大会への意気込み
この様な機会を頂いた事に感謝し、この活動が少しでも多くの方に
役立つ情報として、広く届く事を期待します。
あ
A-6 トヨタ車体株式会社 杉浦 和弥さん
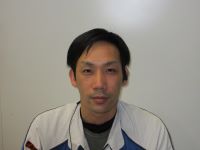
Q1.業務内容と担当業務の経験年数
金型の保守保全・22年
Q2.改善に至るまでの苦労や工夫
今回、取り組んだ改善活動は自動車外板、
アルミ鋼鈑では切断時に必ず発生する切粉を金型清掃と切断面の確認を行い
様々な切断条件の確認を行いトライ&エラーを行い、
他社に赴き良い活動を行っていれば取り入れ、
メカニズムから切断ではなく押して切る方法を取り入れ、
私達のこれまでの経験やスキルだけでは解決できなかった
大きな問題への改善効果を得る事ができた。
Q3.大会への意気込み
プレス金型では固定概念を覆す改善事例です。
今回、優秀改善事例全国大会で自分達が行って来た活動を
発表出来ることを光栄に存じます。
A-7 マツダ株式会社 三浦 美幸さん
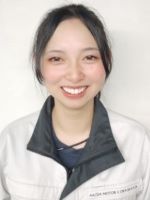
Q1.業務内容と担当業務の経験年数
保全業務・7年
Q2.改善に至るまでの苦労や工夫
新しく状態監視を導入するために設備改造はどうするか、
システム系、ネットワーク系の構築に知識がなく苦労しました。
設備のめざす姿を決め創意工夫でメーカーを巻き込み、
寿命延長・内製化し成し遂げた改善ができました。
Q3.大会への意気込み
自分達の職場がやり遂げた成果を
全国の企業へ知って頂ける機会を頂けとても光栄です。
過去の先輩方の努力・志を受け継ぎ進化させてきた予知保全、
改良保全による設備の信頼性向上の改善事例です。
この活動での私達が行った絶え間ない努力と飽くなき挑戦に着目し
視聴して頂けると幸いです。
A-8 日産自動車株式会社 大下 悠仁さん
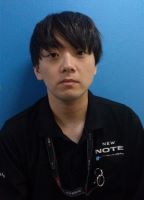
Q1.業務内容と担当業務の経験年数
組付け業務・3年
Q2.改善に至るまでの苦労や工夫
誰が作業しても同じ品質になる受け具を、技術課と連携して作る事が出来た
Q3.大会への意気込み
私たちの取り組みが多くの方に「見て良かった」
と思って頂けるよう心を込めて発表します
B-1 マツダ株式会社 宮田 純次さん
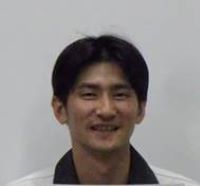
Q1.業務内容と担当業務の経験年数
保全業務・12年
Q2.改善に至るまでの苦労や工夫
故障のメカニズム解明にCAE解析を用いて
機械的弱点部位の診える化にチャレンジしました。
Q3.大会への意気込み
私たちの活動が会場の多くの皆様に伝わり
更なる改善の一助となるように最善を尽くします。
B-2 株式会社三五 矢沢 フェルナンドさん
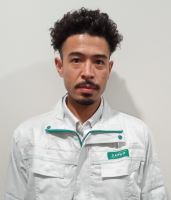
Q1.業務内容と担当業務の経験年数
製造業務・19年
Q2.改善に至るまでの苦労や工夫
対象法ではなく、発生源対策として取り組んだところ。
切りカスに拘り調査追求を実施。
Q3.大会への意気込み
エキマニの圧痕キズ改善について、今回取り組みをいたしました。
参加者の方に理解していただけるように、発表いたします。
今回初参加ですが、優秀改善事例全国大会の場で発表できることを
光栄に存じます。
B-3 株式会社デンソー岩手 佐藤 健一さん
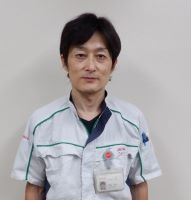
Q1.業務内容と担当業務の経験年数
施設原動保守・30年
Q2.改善に至るまでの苦労や工夫
最初からメンバーの出来ないという固定観念、
あきらめずに説得・挑戦しマインドを変える事が出来ました。
Q3.大会への意気込み
今回の発表で、施設保全の業務を少しでも皆さんにわかって頂ける様に
落ち着いて発表したいと思います。
B-4 愛三工業株式会社 李 裕燦さん
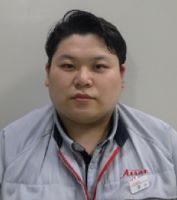
Q1.業務内容と担当業務の経験年数
保全業務・3年
Q2.改善に至るまでの苦労や工夫
紆余曲折したが、関係部署との連携と兆候管理システムの導入により
課題をクリアすることができた。
Q3.大会への意気込み
改善に協力してくれたメンバーの熱い思いが
会場の皆さんに伝わるように全力で挑みます。
B-6 JFEスチール株式会社 中村 祐弥さん
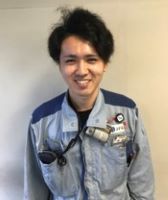
Q1.業務内容と担当業務の経験年数
保全業務・7年
Q2.改善に至るまでの苦労や工夫
一番苦労したところは点検ユニット作成でした。
カメラと照明の位置や重量の検討さらに点検ユニットが回転しないように
ガイドを取り付けるなどして安定した状態で
上げ下げ出来るようにすることが苦労したところです。
Q3.大会への意気込み
初めての参加となりますが、優秀賞を頂けるように精一杯頑張ります!
B-7 敷島製パン株式会社 大城 謙也さん
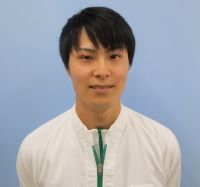
Q1.業務内容と担当業務の経験年数
製造業務・8年4か月
Q2.改善に至るまでの苦労や工夫
製品の向きを変えれば自動位置変えができることがわかり、
その自動化を考えたが、製品に傷が入るという不具合が発生し、
理想的な器具を探すことに苦労した。
Q3.大会への意気込み
私にとって初めての改善事例発表大会が全国大会出場までに至り
とても貴重な経験をさせて頂いています。
私達が取り組んだ改善活動に自信を持って大会に挑みたいと思います。
B-8 株式会社アイシン 都築 拓也さん

Q1.業務内容と担当業務の経験年数
保全業務・10年
Q2.改善に至るまでの苦労や工夫
溶接時の玉垂れ発生状態を見える化することに拘り、
他業種まで巻き込み撮影を成功させ対策に結び付けた
Q3.大会への意気込み
優秀事例に輝くぞ!
C-2 旭化成株式会社 板谷 良樹さん
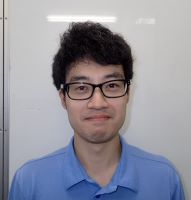
Q1.業務内容と担当業務の経験年数
運転業務・5年
Q2.改善に至るまでの苦労や工夫
運転状況を細かく見たり、反応中のストレーナを開放したり、
サンプリング・分析を繰り返し行い、確認しながら進めました。
Q3.大会への意気込み
改善に関わった皆さんに感謝しながらしっかりと発表したいです。
C-3 豊田合成株式会社 棚橋 進哉さん
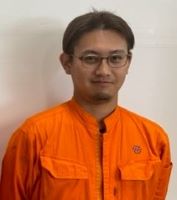
Q1.業務内容と担当業務の経験年数
保全業務・18年
Q2.改善に至るまでの苦労や工夫
ウレタンハンドルを製造する工程において、
長年停止時間・故障件数共にワーストになっていたのが
『顔料詰まり 』でした。今回の改善活動では、
他部署にも協力していただき、
改善したことで目標達成をする事が出来ました。
Q3.大会への意気込み
優秀改善事例全国大会という場で報告出来ることを嬉しく思います。
頑張って報告しますのでご聴講いただけると有難いです。
C-4 トヨタ自動車九州株式会社 竹本 ららさん
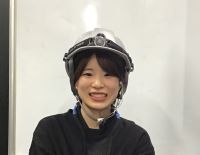
Q1.業務内容と担当業務の経験年数
組立保全業務・4年
Q2.改善に至るまでの苦労や工夫
優秀改善事例全国大会の場で発表できる事を光栄に思います。
私達は普段、設備が万全な状態で可動が維持できるようにする為に
設備の保守、保全を行っています。
その中でも長時間停止を未然に防止したい思いから、
問題が顕在化する前にいち早く察知する『兆候管理』という点に着目し、
今回小集団活動で改善を行いました。
動いている物の状態監視に過去に実績のないAIカメラを使用するという
新しい試みに踏み込むのは苦慮する点は多々ありましたが、
いち早くお客様の元にレクサスを提供したい、
この思いひとつで設備兆候管理を実現化させる事ができました。
Q3.大会への意気込み
過去10年間分の停止内容を一から解析し、
保全のみならず他部署やメーカーを巻き込み一丸となって改善した内容に、
ぜひ注目してお聴き頂けたらと存じます。
C-5 愛知製鋼株式会社 本郷 雅人さん
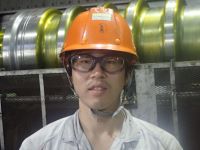
Q1.業務内容と担当業務の経験年数
ロール旋盤業務・6年
Q2.改善に至るまでの苦労や工夫
スラストリング肉盛りでは、材質による歪み、
その他苦労はありましたが、技能士の大川さん、
また専門保全組への協力を依頼し最後までやりきりました。
一番は『失敗を恐れず、自分達でやってみよう』の気持ちで
最後まであきらめず、全員参加で目標を達成する事ができました。
Q3.大会への意気込み
会場の皆様全員に自分達の頑張りが伝わるように発表します
C-6 株式会社日本触媒 戸髙 祐幸さん
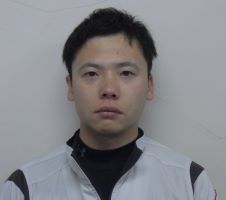
Q1.業務内容と担当業務の経験年数
製造技術・5年
Q2.改善に至るまでの苦労や工夫
機械学習・統計解析とは?というレベルからデータ解析をスタートし、
自部門を飛び出して協力体制を築き、課題解決に至りました。
本件を通して、製造現場における具体的な
データ活用法を学ぶことが出来ました。
Q3.大会への意気込み
他社様の事例を見学させていただき、問題を捉える視点・課題解決への
切り口といった部分を自社に持ち帰っていきたいです。
併せて、弊社の発表事例が皆様の改善・改良活動の糸口になれば幸いです。
C-7 トヨタ車体株式会社 阪西 奏一郎さん
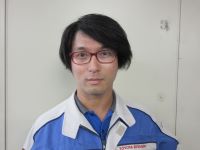
Q1.業務内容と担当業務の経験年数
保全業務・1年
Q2.改善に至るまでの苦労や工夫
化学的な部分に手を伸ばした事、長期間の対応に苦労がありました。
費用低減のための選定と移設をしています。
Q3.大会への意気込み
サークル最後のテーマを大舞台で発表できることを光栄に感じます。
質問あれば遠慮なくお聞きください!